(Multiple) Dividing Wall Columns
Distillation is the most widely used separation technology in the chemical industry and covers approximately 3% of the total energy consumption. Reducing this amount and thus also the environmental impact of distillation is the core of our research. For this purpose, we investigate a special kind of distillation column called Dividing Wall Column. These allow the separation of ternary mixtures into the pure components in only one column shell by the application of a partitioning wall inside the columns. This results in considerable reductions in capital and operational costs and energy consumption/operational costs, accordingly these columns are nowadays widely applied in chemical industry and can be considered as a mature technology. By adding additional partitioning walls this concept can be extended to quaternary separations. Further reduction of costs and environmental impact becomes likely. However, the complexity of these units is highly increased and none of these Multiple Dividing Wall Columns have ever been realized.
Our work focuses on the fundamental understanding of Multiple Dividing Wall Columns based on rigorous modeling, simulation and multi criteria optimization. After 4 years of development we were able to build the first multiple dividing wall column on mini-plant scale an started operation in November 2021.
The project is devided in several sub-projects addressing questions of modeling and simulation of the dynamic beahaviour in particular, mathematical optimization (multi criteria optimization) and practical aspects of design, control and operation of the column.
Funded by: Deutsche Bundesstiftung Umwelt (DBU), Az.: 34815/01; Deutsche Forschungsgemeinschaft (DFG), Az.: 665461
Involved Members: Dr.-Ing. Lena-Marie Ränger, M.Sc. Lea Trescher, M.Sc. Yannick Waibel
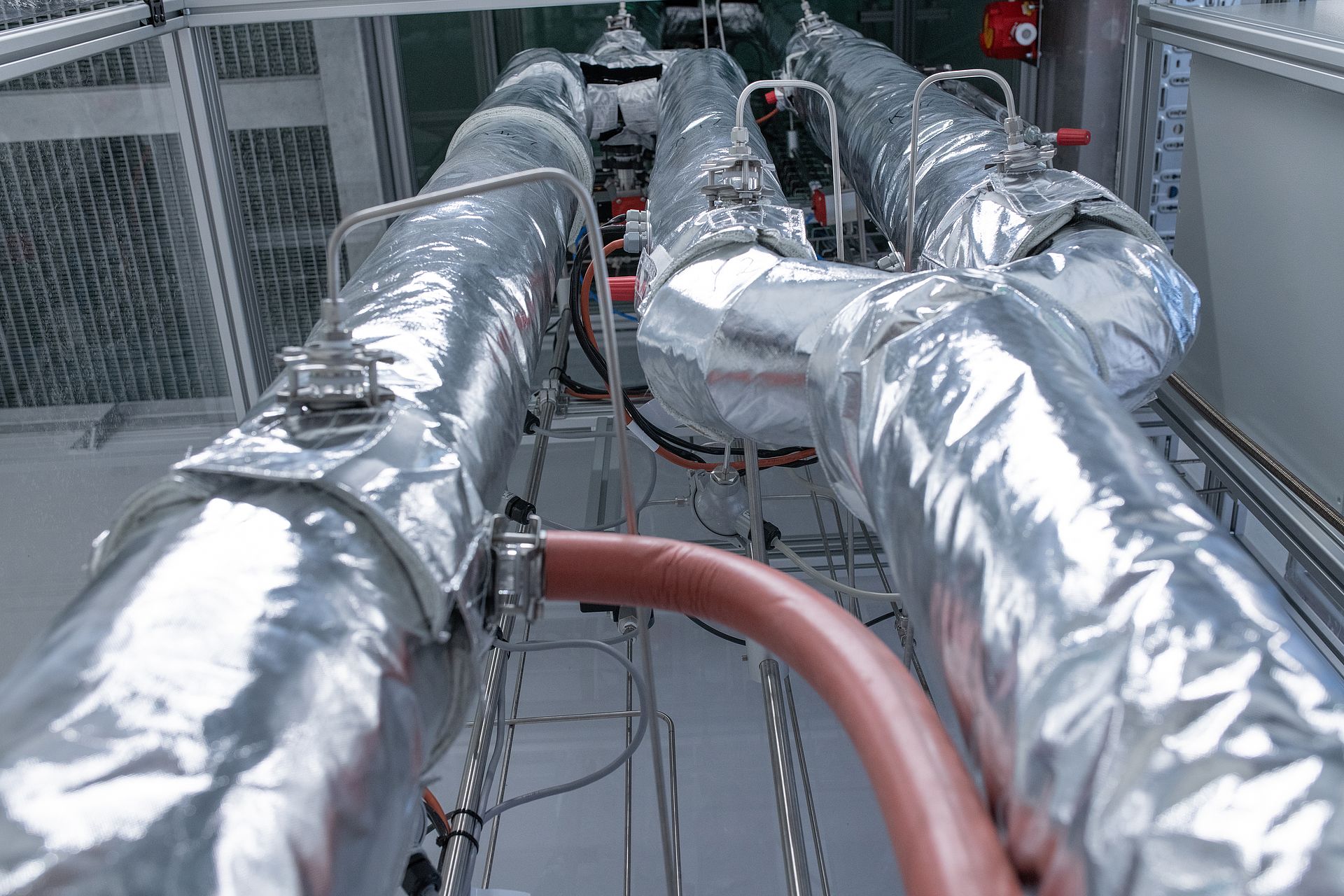
Additive Manufacturing (3D-printing) in Process Engineering
Additive Manufacturing (3D-Printing) allows the generation of structures that cannot be made by conventional manufacturing processes. This opens the window to entirely new concepts in thermal process engineering. We are aiming to improve the perfomance and scalability of laboratory equipment with special focus on distillation. Our packings show good performance in terms of separation efficiency (HETP), pressure drop, reproducibility and liquid distribution. In particular, we succeeded in developing packing structures that exhibit virtually constant separation performance over a wide range of gas loading. These packings are therefore well suited for the application of scalable laboratory columns. The diameter of columns we use in the lab for sclae-up experiments can be reduced to DN20.
Our developments include all relevant components of columns (beside the packing): jacket, liquid distributors, sampling trays, side draw trays etc. All components are computer generated and can be adapted quickly. The characterization is done on the basis of CFD simulations and in self-developed test rigs in the laboratory.
In DFG-funded projects, we are working on the development of a scalable, additively manufactured dividing wall column for laboratory applications and, in a second project, on the behavior of liquids on printed surfaces.
We are also developing specific technology to measure contact angles on printed surfaces.
The group has its own SLS and SLA printers and extensive analysis technology at its disposal.
Funded by: BASF SE (Ludwigshafen), Deutsche Forschungsgemeinschaft (DFG) Az. 510113776 and Az. 533252297 and from own financial resources.
Involved Members: M.Sc. Adel M. Ashour, M.Sc. Dennis Stucke, M.Sc. Chiara Lukas

Extraction and Rotating Extraction Centrifuges
Rotating extraction centrifuges are in the focus of this project. These devices allow a very efficient separation of liquid phases due to high g-forces. Within a relatively small volume extraction centrifuges realize one theoretical stage. Our research aims to establish these modules in the context of flexible and modular production facilities as well as the intensification by performing reactive-separations. A current focus is the study and understanding of the complex fluid dynamic processes within the apparatus.
We are also working on fundamental issues relating to extraction and the determination of liquid-liquid equilibria. For example, we are working on the expansion of graphical methods such as the determination of minimum and maximum solvent to feed ratios.
Funded by: German Scholar Organization (CSO/CZS 21) and own financial resources.
Involved Members: M.Sc. Zaid Hamamah
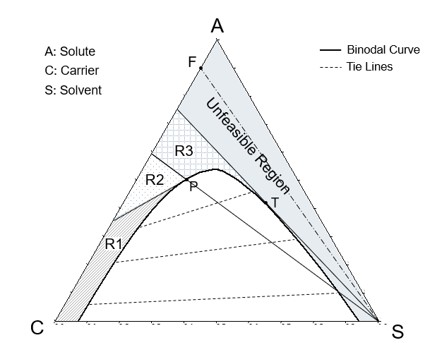
Industrial Side Projects
We are trying to close the gap between research and industrial application and are thus open for cooperation projects with industrial partners having questions in the field of thermal separation processes. In addition to our core projects, we have therefore already dealt with issues in the areas of absorption, reactive extraction, food process engineering and more. So do not hesitate to contact us, most likely we can find a solution for your problem.
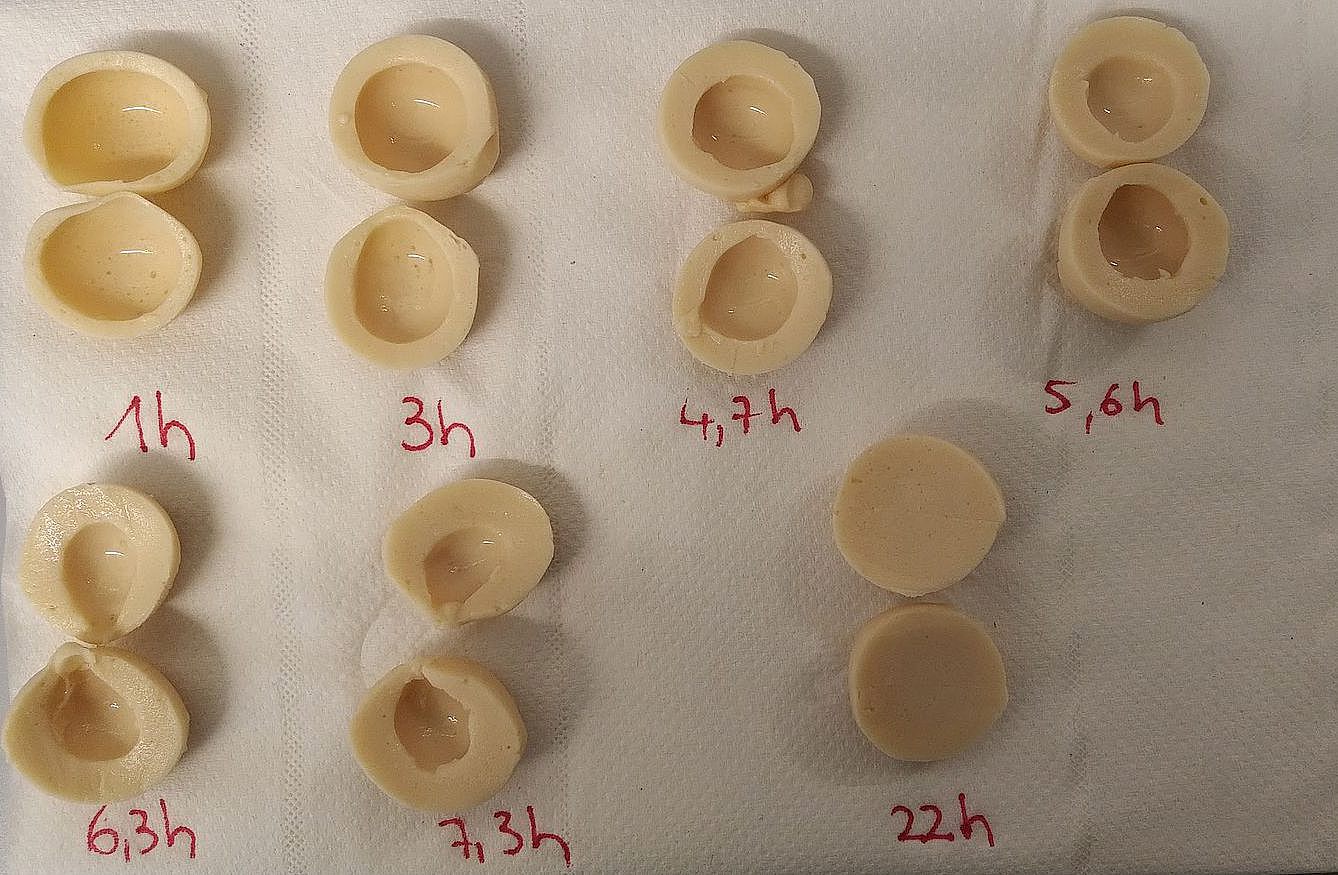